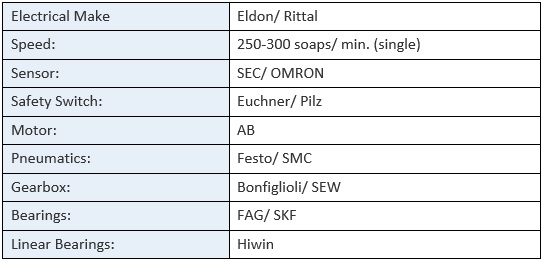
Vertical Case Packer
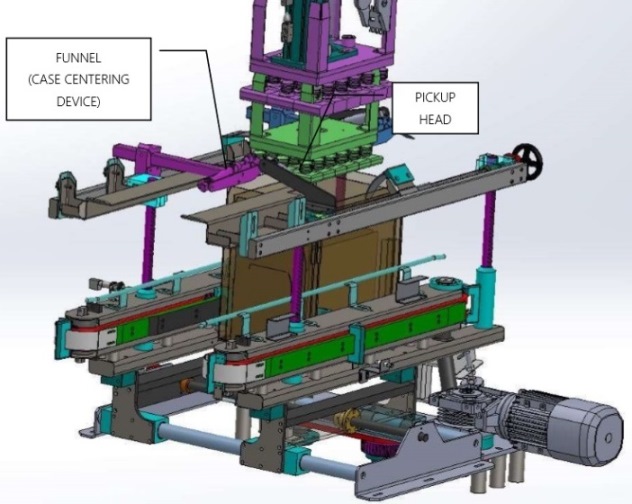
Overview
Cases Erected by Case erector will travel on a case conveyor & will stop at case filling station. The flaps of the case at filling station will be opened with the help of a pneumatically operated flap opening device so that the flap does not obstruct while case packing.
Cases erected by Case-Erector will travel on a case conveyor & will stop at case filling station. The flaps of the case at filling station will be opened with the help of a pneumatically operated flap opening device so that the flap does not obstruct while case packing.
The Cartons of indulekha oil from the upstream machine will be transferred to EOL product conveyor which is equipped with a suitable product stopper & a servo driven pusher assembly. Pusher will push the cartons towards collation table/ C plane. Collation table/C plane is the matrix formation place in the case packer. Pusher will count the push cycles required to form suitable matrix to pack, this value can be adjusted through HMI, & on completion of required push initiate a command to start the vertical axis cycle. The vertical axis of the machine is a servo driven assembly fitted with a suitable gripping head. The gripping of the gripper is through vacuum for an efficient grip. Once the gripper grips the matrix of combi packs, the C plane/ collation table, which is driven by a servo motor, moves & create a passage for the vertical axes to go down. The vertical axes then go down & places the gripped matrix in to the CFC. This cycle continues till the required bundles are placed in to the CFC. On completion of CFC filling, a new empty case is placed beneath the filling station. The number of layers n the CFC can be adjusted through HMI by operator.
On completion of filling cycle, the box will be pushed to the next station where customer’s case sealer machine will seal the top side of the box. If required an Online date coding machine can also be installed on the case sealing machine for date & batch coding activity.
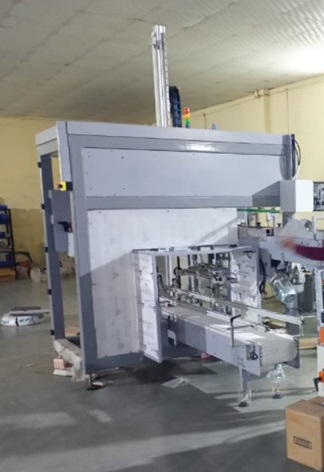
On completion of filling cycle, the box will be pushed to the next station where customer’s case sealer machine will seal the top side of the box. If required an Online date coding machine can also be installed on the case sealing machine for date & batch coding activity.
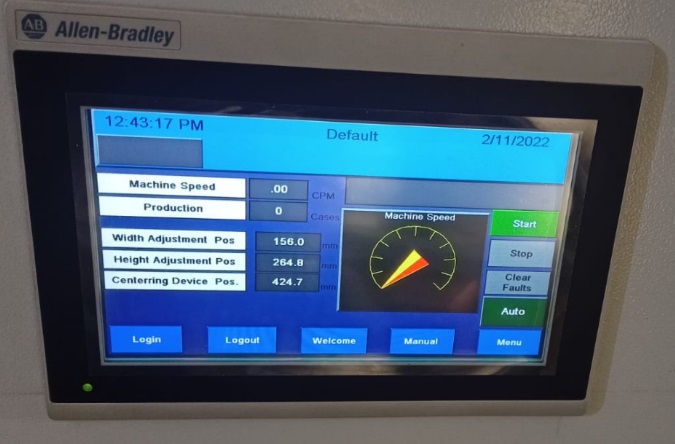
- Clear, high visibility guards - electrically interlocked to stop the machine when opened.
- Continuous operation.
- Compact size.
- Wide case range.
- Low maintenance.
- Stainless steel frame construction.
- Powered flap tucker folds trailing inner flap.
- Contoured cast aluminum flap folders fold outer flaps.
- Tape roll is easily accessible for quick replenishment.
- Independently adjustable leveling footpads.
- Sealed bearings minimize maintenance.
- Automatic water eliminator keeps airline dry.
- Tape sealing only.
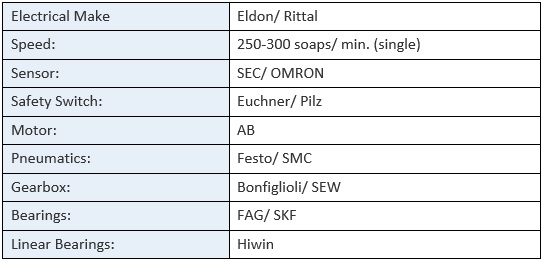
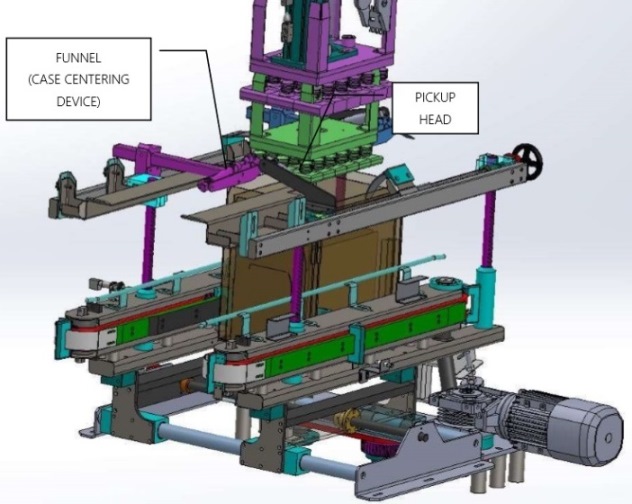
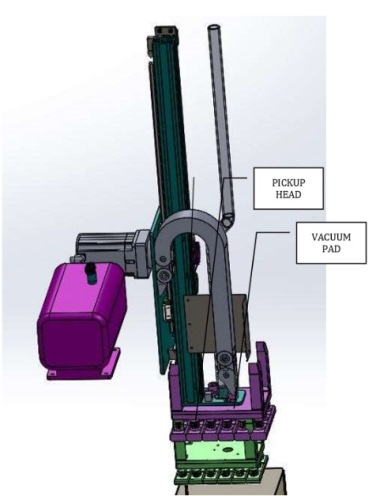
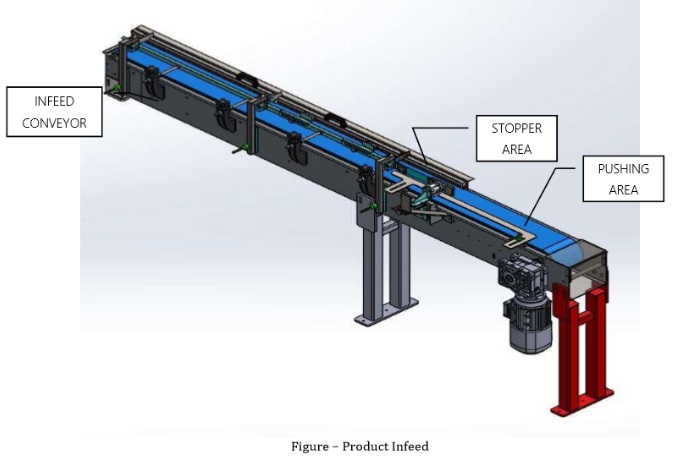
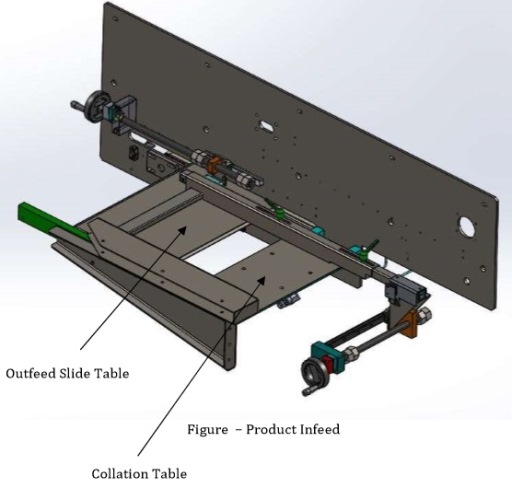
The product must be fed on the feeding conveyor in a single lane. At the beginning of the new cycle, Infeed gate is closed allowing product to accumulate until minimum sensor get activated. Once both minimum sensors are active, Infeed gate is given a signal to open allowing the product to continue to the pushing area. Sensors fixed for sensing the product senses the product & gives a signal to close the infeed gate. The product is pushed towards the collation table to form a required matrix. Cycle repeats till the required matrix is formed on the accumulation table. After a long push the product is transferred to C plane area & pick up activity is initiated. The pick-up head equipped with vacuum gripping head assembly moves down to pick up the collation. Once the product is gripped properly, the slide table opens allowing the movement of vertical axis head for depositing the gripped product in the box. The product is placed at a pre-programmed height in the case depending upon the layer value fed in HMI. Filled case is moved out & a new case comes in position for packing. This cycle continues.